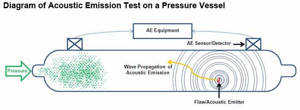
High pressure cylinders are qualified for use at the time of manufacture. The qualification is performed to help ensure the cylindes are manufactured to meet regulatory requirements. Once cylinders enter service they require periodic visual inspections and requalification’s to help ensure their continued safe use and operation. A cylinder is exposed to numerous environments and conditions that may cause the cylinder to corrode or weaken. To help ensure the continued safe operation of cylinders, regulations require that cylinders shall be submitted for periodic requalification. There are three common requalification methods used on high pressure cylinders. Volumetric Hydrostatic Test (VHT) more commonly referred to as hydrostatic requalification, Ultrasonic Examination (UE) and Modal Acoustic Emission (MAE). Each of these methods of requalification determines a quality. Each of them also has pros and cons.
The most commonly used method is VHT, which we will refer to using its more common name, hydrostatic or hydro. In this process the de-valved cylinder is filled with water and placed in a water filled jacket. The cylinder is pressurized to 166% of its working pressure or 5/3rds. The purpose is to, determine the elastic capability of the cylinder and ultimately, will it return to within a percentage of its original shape. A solid wall (steel or aluminum) must return to within 10% of its original shape. A composite cylinder must fall within the tolerance specified in the Special Permit. If the cylinder does not return to within its tolerance, it must be condemned. If it passes, then the Hydro tester marks their Requalifier Identification Number (RIN) with the month and year the test was conducted. See example below:
The pros of a hydrostatic test is that the equipment and training is common. Somebody requiring a hydro can search locally and usually find several hydrostatic requalifier’s in their area. This form of testing has also been around for decades and has a proven safety track record. The cons of a hydro are that the cylinder valve must be removed, and the cylinder emptied of their gases. Another concern is that water is added to the cylinder which will expose the cylinder to moisture and potentially add other contaminates.
Another type of cylinder requalification is the Ultrasonic Examination (UE). During a UE the cylinder is placed on a platform. The platform is outfitted with sensors designed to read the thickness of the cylinder walls. The angle of the sensors determines what areas of the cylinder is being inspected. The cylinder will begin spinning around the sensors. A couplant, such as oil or water, is used between the cylinder and the sensor to provide consistent readings. As the cylinder rotates, the sensors send the signals to a computer attached to the platform. A trained technician interprets the results and determines if any part of the cylinder wall is thinner than a safe limit. The cylinder is accepted or rejected based on the stated design thickness of the cylinder wall. If the cylinder passes, the RIN holder applies their marking (as shown above) followed by “UE” to indicate the cylinder was qualified using an ultrasonic examination.
The drawbacks to a UE are the cost of the instrument and the necessary training to be able to operate the equipment properly. Another concern with UE is that it may only evaluate the wall thickness of the cylinder, ignoring cracks and other concerns. UE does not determine if the cylinder can actually hold pressure or if the interior of the cylinder meets the standards for the gas/application. The benefits of the UE are that the cylinder valve can remain in place and the contents do not need to be emptied for the testing procedures. The cylinder is not stretched or pressurized to gather the results. The other benefit is that UE gives a great indication of any possible corrosion since it focuses on the overall thickness of a cylinder.
The third type of requalification is Modal Acoustic Emission (MAE). MAE is becoming readily available because it checks for flaws using an acoustic wave, which can locate flaws within a cylinder without having to drain the cylinder of its content. MAE testing requires a group of sensors being placed on the cylinder. The sensors are attached to a computer which adjusts the sensitivity based on outside noises and anomalies. The cylinder is filled with its gas content to 110% of its working pressure. As the pressure increases the sensors listen for any stress wave which can be generated in a flawed cylinder. This is very helpful when testing composite cylinders since it can register damaged fibers within a composite. If a flaw is found on the cylinder, then a UE examination may be required to determine the exact location and issue of the damage.
MAE testing is being used to determine if composite cylinders, currently limited to 15 years of service life, can be extended beyond 15 years. Certain companies have been granted Special Permits (SP) to conduct MAE testing and extend the service life of a composite cylinder. If it passes a specific test, the cylinder is affixed with the company specific SP# and can remain in service for up to an additional 5-year cycle. The maximum service life of any composite cylinder is 30 years. If the cylinder passes a MAE examination, then the three letters “MAE” are placed after the RIN after requalification.
The benefits of a MAE examination is that the cylinder does not need to be drained of the existing contents. It is only pressurized to 110% of its working pressure and the testing can be conducted on site, no need to take the cylinder to a specific location. The drawbacks are the cost of the equipment and the required training and skill level of the technician. Another issue of MAE testing is that if a flaw is located, another test may need to be performed to locate and assess the specific damage.
When checking a cylinder for safe operations it is beneficial that there are numerous techniques at a facilities disposal. Due to the varied nature of a cylinders use, and location of operation, not one single test can be expected to determine if a cylinder is safe. All the tests require a trained technician on the specific equipment. Using any of these unique tests still require a VISUAL INSPECTION of the cylinder. The best way to ensure safety is to use modern technology and a good old-fashioned visual assessment.
Copyright © [hfe_current_year] [hfe_site_title] | Powered by [hfe_site_title]