Visual Inspection Stickers – Who do you trust?
Let’s begin this article by stating that there is no United Sates federal law mandating annual visual inspections in the SCUBA industry. The federal law mandates a hydrostatic requalification for a cylinder, but nothing on an annual basis. The annual inspection program in the SCUBA industry was first reported in 1969 with a study conducted by the University of Rhode Island (URI). In the URI report they were researching safety concerns and documented the following in the study:
One of these organizations, the National Association of Skin Diving Shops. (NASDS) does have a valuable cylinder safety program, which it is trying to promote. This program is called the Visual Inspection Protection program (VIP). Under the program each diver has his SCUBA cylinder visually inspected once a year. The diver is charged a small fee of about $1.50; and in return, he receives the satisfaction of knowing the internal condition of his cylinder. In addition, if his cylinder is free from damaging internal corrosion, he is given a VIP sticker (Fig. 2) which is good for one year and enables him to save 25 cents on each air fill.
The NASDS program used a VIP sticker to show the cylinder was inspected and offered a discount air fill for having the cylinder inspected. The report does not state who issued the visual inspection stickers, or the training of the person inspecting the cylinder. That same problem continues to this day.
Visual inspection stickers commonly have a shop’s information and logo for promotional purpose. They place dates on the sticker and indicate when it was inspected, and as a reminder for when the next inspection is due. I would assume that most shops have inspection procedures in place and have trained their staff in proper inspection protocols. Why would they not? They are inspecting a cylinder that they will likely be filling, and they want to ensure its safety. If a problem occurs it affects their shop and their employees.
What happens when that cylinder is taken to another shop to be filled with a compressed gas? This shop is not aware of the training of the inspecting facility, they might not know the other facility, or they might feel that they are a competitor and look upon the visual inspection sticker with distrust. If this occurs, and one shop does not accept another shop’s sticker, there is only one concerned person; the cylinder owner. The cylinder owner was following the rules of the industry and getting their cylinder inspected annually. They went to the most convenient location to use their services. How was the customer to know that one shop may not trust another shop?
The SCUBA industry must continue encouraging the customer to obtain their annual inspections. SCUBA cylinders are exposed to many hazards that may cause concern during the filling process. To keep everyone safe the SCUBA cylinder should undergo a regular inspection, sometimes more frequently than every 12 months. If the cylinder has been exposed to a hazard it might need more frequent inspections. The customer must be educated and encouraged to have their cylinder inspected at any time an issue arises.
To keep the cylinder owner confident in an annual inspection program they must have some assurance that their cylinder was inspected by an individual with formal training. They must also be confident, that wherever they take their cylinder, that it will be filled because they did have a visual inspection completed. It is also up to the fill station to be confident that if another location inspected the cylinder that it is safe to fill.
The trust begins with proper training for the facility issuing the visual inspection. If they have sent their employees through a formal program a card and or certificate should be issued proving that they completed a training program. That certificate or card should be displayed prominently on the walls for everyone to see. A simple step like this will ensure the customer that their cylinder is being inspected by a trained individual and the facility issuing the visual sticker is qualified to do so. That way, when the customer goes to a fill station who questions the validity of the sticker, the customer can state that they saw the training credentials that stand behind the Visual sticker. If the fill station is still in doubt they can contact the other facility and request the training date and certificate of the inspector who conducted the formal inspection. If these steps are followed the fill station should honor the visual sticker to ensure that the consumer does not lose faith in the visual program.
The sticker needs to be able to handle the extreme environmental conditions, and these types of stickers do not come cheap. Some shops are unable to afford their own personal stickers with their facilities name, address and logo. They may need to purchase generic stickers from outside sources at an affordable rate. In this circumstance the fill station would have no idea who to call to verify the training since there are no names or phone numbers on the sticker. Because of this, it is important that a sticker without facility information have the name of the inspector listed on that visual sticker. That will help assure a fill station technician that the cylinder was properly inspected.
An example of such a sticker (see below) states: This cylinder was inspected by a trained inspector and complies with the appropriate government safety regulations or gas industry standards of its stated material
The statement does a number of things. It ensures that whatever the composition of the cylinder, (steel, aluminum or composite) it was inspected to that specific standard. It also states that the person inspecting the cylinder was trained. How can this be verified? By the signature of the inspector at the bottom, stating their inspector number or qualification. The person signing the sticker is signing a declaration that they were properly trained. That helps the fill station technician understand that someone is placing their actual name on the item they inspected.
There is no way to guarantee that someone placing a visual inspector sticker on a cylinder was properly trained, or paid attention during their class. Some persons might even go so far as to make up a sticker and make false claims. However, we as an industry need to start trusting one another, to not trust someone because they are a competitor and we don’t like them is unprofessional. All that does is make the consumer uncomfortable with the entire visual inspection program.
The fill station or store should always check for proper cylinder markings and a current inspection sticker prior to filling a cylinder, trusting that the store, person or inspector who placed the sticker on the cylinder was properly trained. If the technician has a doubt about a cylinder’s safety, they can always insist on performing their own inspection. It is up to them if they are going to charge the consumer for this added service or simply perform it as a courtesy for the sake of safety. If they are refusing to fill a cylinder simply because the visual inspection sticker does not meet their personal needs, they should have the courtesy of explaining that to a customer. The customer deserves an honest answer of why the technician will not fill a cylinder. Simply stating “it’s not safe” with no justification is poor customer service and not an acceptable response.
Always be safe filling a cylinder and question the customer if something appears wrong or unsafe about the cylinder. But check your unsolicited opinions at the door so you don’t start eroding the consumer’s faith in the very safe program of annually inspecting our SCUBA cylinders.
Author – Don Kinney
About the author: Don Kinney is the owner of Cylinder Training Services (www.cylindertrainingservices.com). He started formally working with and filling cylinders in 1991. With his background in public safety he continued to gain knowledge in the field of high pressure cylinders and began to develop training programs. He has developed programs for PSI/PCI including; Eddy Current testing (2003), SCBA, Fire Department (2004) and their Fire Safety Seminar program (2004). He went on to develop his own visual inspection program covering cylinders, valves, cleaning and compressors in 2011. At this time he realized that inspectors needed a source for affordable and high quality inspection tools. His tools are designed for the high pressure cylinder industry, and assist them in determining damage and ensuring cylinders remain safe. In 2014 he developed an inspection program for International Training (ITI) where he published a manual and developed an on line training program. Don continues to dedicate himself to safety in the high pressure cylinder industries. He prides himself on understanding the clients and their needs and coming up with a safe and useful training program designed to keep them safe and save them thousands of dollars.
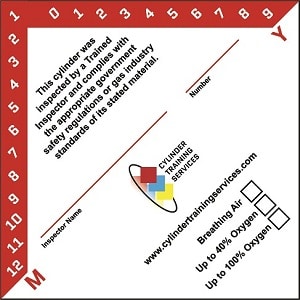